How are Kalsi Seals® used for high pressure?
Categories of high pressure rotary seals
There are four basic categories of Kalsi-brand rotary seals that are used for retaining high differential pressure. Each of these seal categories is tailored to a different hardware arrangement. The first category is the broadest and includes many of our solid cross-section direct compression seals, such as our Wide Footprint, Hybrid, Enhanced Lubrication™, and Plastic Lined™ high pressure oil seals. The second and third categories are lip seals: our KLS® seals and washpipe packing. The fourth category is our BDRP Seals™. What follows is a brief summary of each high pressure seal category.
Category 1: Solid cross-section high pressure oil seals with waves on the pressurized lubricant side
Most Kalsi-brand rotary seals that are used for retaining high differential pressure have a solid cross-section, are designed to retain a pressurized lubricant, and have what are known as hydrodynamic waves that face the pressurized lubricant. These waves pump lubricant into the dynamic sealing interface when the shaft rotates. What this means in terms of performance is reduced friction, wear, and seal generated heat. The reduced seal temperature means better retention of material properties, including high pressure extrusion resistance.
When this type of rotary seal is used to retain a pressurized process fluid that is not a lubricant, a pair of oppositely facing seals is used, and lubricant is provided between them that is pressurized to a value equal to or greater than the pressure of the process fluid. With this type of arrangement, one rotary seal serves as a partition between the process fluid and the seal lubricant, and the other retains the lubricant pressure. Both rotary seals are mounted in housing grooves and compressed radially against the rotatable shaft. The system that provides the pressurized lubricant also accommodates the hydrodynamic pumping related leakage of the Kalsi Seals.
The object of any high pressure rotary seal is to prevent gross fluid loss through the clearance gap that exists between a machine housing and a shaft. The smaller the clearance gap, and the less it changes due to factors such as shaft runout and deflection and housing pressure breathing, the better the seal can withstand high differential pressure — provided the shaft doesn’t rub on the housing and generate enough heat to damage the seal. Because of the critical nature of the clearance gap, special hardware has been developed that allows the gap to be optimized, including laterally floating metal backup rings and laterally floating seal carriers. If desired, pressure capacity can be further increased by pressure staging.
The ultimate pressure capacity of a Kalsi-brand rotary seal depends on several factors, such as the type of seal carrier and the clearance gap size that are used, the seal material, the rotary speed, the aggressiveness of the hydrodynamic waves, the ambient temperature, the degree of available heat transfer, and the required seal life. As an example of the results that can be achieved, we tested 2.75″ (69.85mm) Plastic Lined Kalsi Seals™ at 7,500 to 7,800 psi (51.71 to 53.78 MPa) and 252 feet per minute (1.28 m/s) for 1,000 hours. The seals were still in excellent condition at the end of the test. The ISO 150 viscosity grade seal lubricant was maintained at 130°F (54.44°C) by a small amount of fluid circulation inside the hollow shaft. As another example, 4.50” (114.30mm) Super Wide Plastic Lined Seals™ survived hundreds of hours of operation with 10,000 psi (68.95 MPa) at 141 to 206 feet per minute (.72 to 1.05 m/s). If you are wondering where to obtain oil seals with true high pressure capability, your search is over.
Category 1 Kalsi Seals are available in a variety of materials and high-pressure shaft seal designs. Seals with plastic-lined construction have the most pressure capacity, followed by seals with Dual Durometer™ construction. For a complete listing of all our seal material options, visit our materials web page. Our rotary seal handbook provides extensive information on the various seal materials and geometries we offer, and provides detailed information about how to implement our high pressure oil seals in various types of rotating machinery, such as rotary control devices (RCDs), hydraulic swivels, mud motors, and side entry swivels. For additional information, call us at 281-240-6500 today and discover why we are a leading high pressure oil seal supplier.
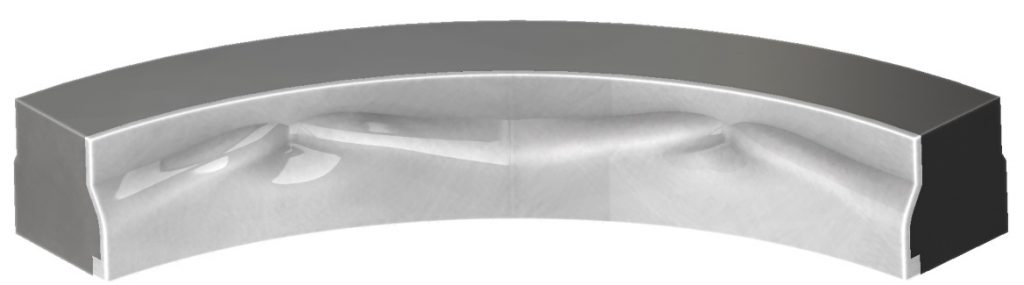
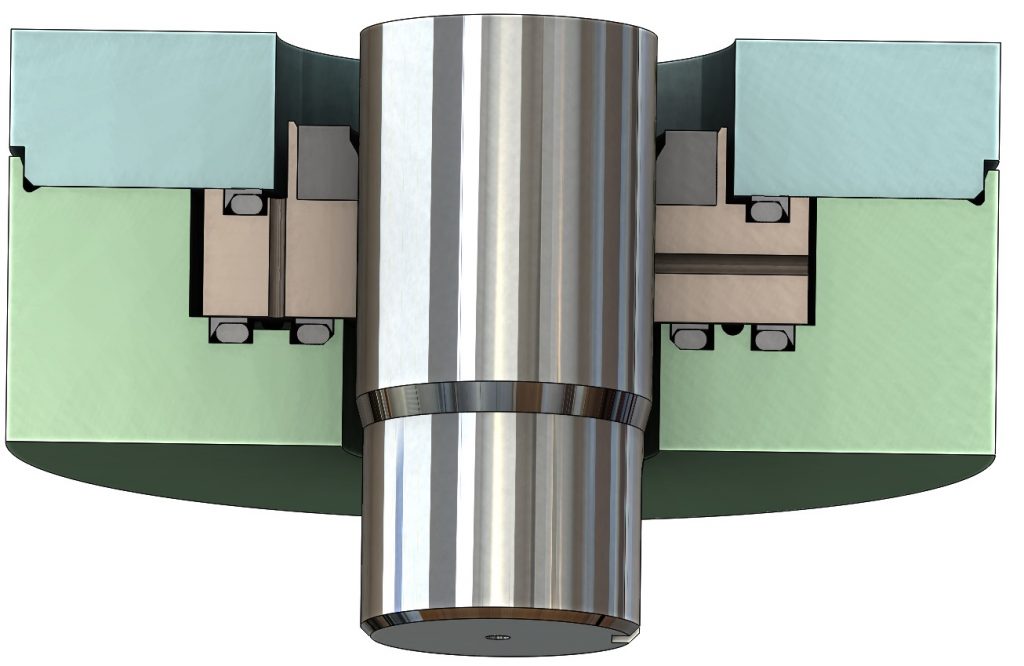
Category 2: KLS high pressure lip seals
KLS seals are spring-loaded high pressure lip seals that incorporate hydrodynamic waves at the low-pressure end of the seal body. The spring end of the seal faces a pressurized process fluid. The wave end of the seal faces an unpressurized lubricant, such as the bearing lubricant of a machine assembly and is supported by a housing wall. Pressure forces the waves into contact with the shaft. When the shaft rotates, the waves force lubricant into the dynamic sealing interface, reducing friction and wear.
If the process fluid contains abrasives, a pair of KLS seals are preferably used, and a barrier lubricant is provided between them that is balanced to the pressure of the process fluid. With this arrangement, the inboard KLS retains the differential pressure and lubricates and flushes the outboard KLS. KLS seals were originally designed as RCD seals for oilfield RCDs that have unpressurized bearing lubricant. Chapter E6 of our rotary shaft seal handbook details how to implement them in such RCDs.
KLS high pressure lip seals have been tested with 1,000 psi (6.89 MPa) at 543 feet per minute (2.76 m/s), and have been tested with 1,500 psi (10.34 MPa) at 137 feet per minute (0.7 m/s).
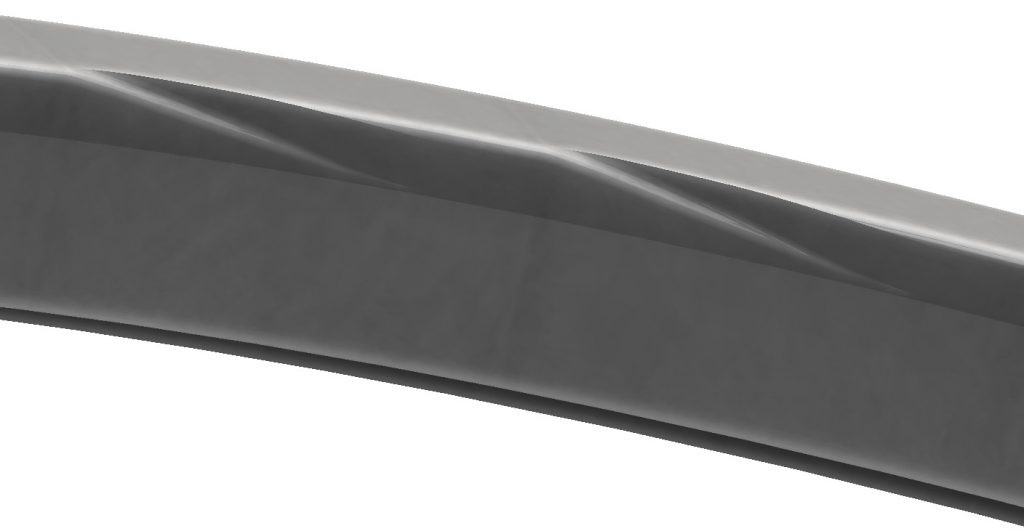
Category 3: Kalsi washpipe packing
Kalsi washpipe packing is interchangeable with the conventional packing that is used in the washpipe assemblies of oilfield power swivels and top drives. Like conventional packing, it is supported by and clamped between form-fitting metal spacers. Kalsi packing incorporates hydrodynamic waves on the low-pressure end of the dynamic sealing lip. Lubricant is provided to these waves by the conventional re-greasing operation. When rotation occurs, these waves help to lubricate the most highly stressed portion of the packing, reducing friction, heat, and wear. We provide hardware-related guidance to organizations who use our high pressure washpipe packing to help them make improvements that promote maximum performance.
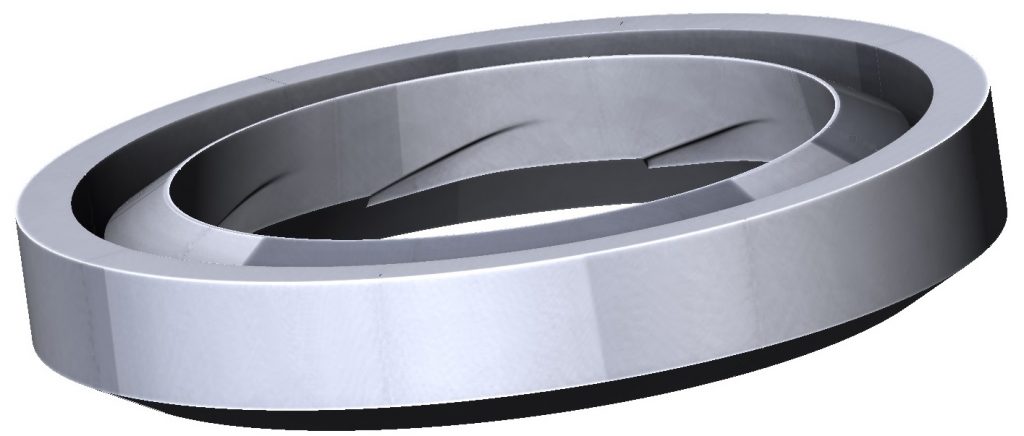
Category 4: BDRP-brand rotary seals
BDRP-brand rotary seals have an elastomer body with an integral plastic lining that incorporates aggressive hydrodynamic waves that allow the seal to hydroplane on a lubricant film during either direction of rotation. BDRP seals are designed to serve as hydraulic swivel seals and can seal lubricant pressure acting in either axial direction. They are simply installed in a housing groove and compressed radially against a rotatable shaft. In the same manner as conventional swivel seals, pairs of adjacent seals are used to define hydraulic channels between the housing and the shaft. BDRP seals are also useful as RCD seals in RCDs with unpressurized bearing lubricant when combined with the lubricant recirculation valve described in U.S. Patent 10,435,981. Chapter E7 of our seal handbook describes how to implement BDRP seals in RCDs.
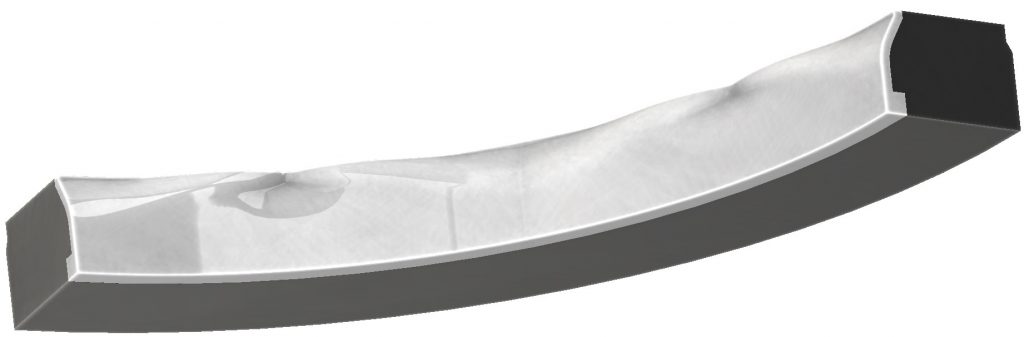
Contact us to discuss your high pressure rotary shaft seal requirements
As a result of our pioneering research in the field of hydrodynamic lubrication, Kalsi Engineering is a world leader in high pressure rotary shaft seal technology. Contact us today for a quote, or to discuss your application. For existing sizes and styles of Kalsi Seals, see our shaft seal catalog. For ordering instructions, click here.
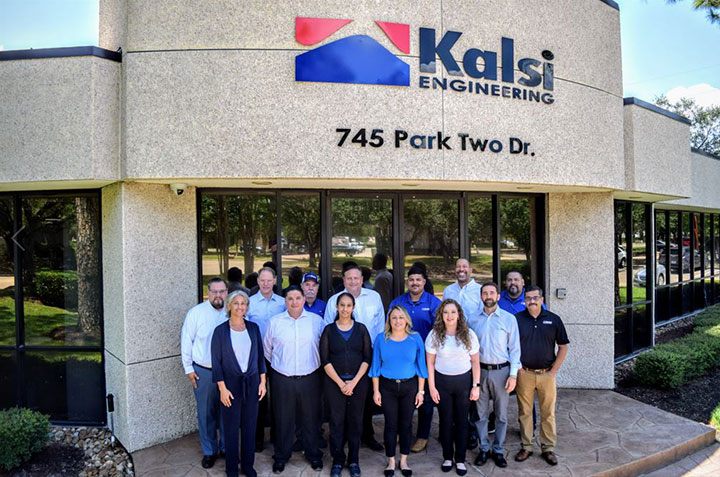