Extreme-Pressure Side Entry Hydraulic Swivel Design
Introduction
Side entry hydraulic swivels communicate hydraulic fluid pressure radially between a mandrel and a housing that are relatively rotatable with respect to one another.
Kalsi Engineering offers two basic types of high pressure seals for side entry hydraulic swivels. Both types incorporate hydrodynamic waves that pump a thin film of hydraulic fluid between the seal and the mandrel during rotation, reducing friction, wear, and seal generated heat.
For pressures in the 1,000 to 1,500 psi (6.89 to 10.34 MPa) range in conventional swivel arrangements, we offer the BDRP Seal™, which accommodates hydraulic pressure acting in either direction. This allows three rotary seals to define two hydraulic circuits, four rotary seals to define three hydraulic circuits, etc.
We also offer rotary seals that can accommodate much higher hydraulic pressure, but only in one direction. These seals, known as Plastic Lined Kalsi Seals, require that each hydraulic circuit be defined by a separate pair of rotary seals. Pressure capacity is dependent on hardware design, mandrel diameter, and surface speed. In a 4.50” size using the best hardware design practices, 10,000 psi can be accommodated for hundreds of hours at 175 sfpm. This web page introduces the best practices for sealing extreme pressure in a side entry hydraulic swivel.
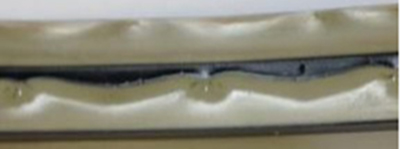
High pressure hydraulic swivel design challenges
One of the most crucial high pressure swivel design factors is the radial extrusion gap clearance between the housing and the mandrel at the rotary seals. For the best seal performance and life, this clearance must be as small as possible without risking heavily loaded housing-to-mandrel contact. Excessive clearance accelerates pressure-related seal extrusion damage. If the clearance is too small, contact between the housing and mandrel may produce enough friction to damage the mandrel, housing, and seals, and cause failure.
A related challenge is pressure breathing, where hydraulic pressure causes components to change dimensions. In conventional swivel designs, pressure breathing increases bearing clearance and extrusion gap clearance, which increases the demand on the swivel seals.
Kalsi Engineering provides a solution, described below, that counteracts pressure breathing and minimizes extrusion gap clearance while avoiding heavily loaded housing-to-mandrel contact.
Designing a side entry hydraulic swivel for extreme pressure surface
The figure below illustrates a single circuit side entry hydraulic swivel for handing extreme pressure. The design is easily expanded to include more than one hydraulic circuit.
The hydraulic circuit is defined by a pair of Plastic Lined Kalsi Seals supported by our patented mandrel-guided floating metal backup rings. Axial hydraulic force balance allows the backup rings move laterally to accommodate misalignment and follow dynamic runout of the mandrel. Radial pressure balance makes the backup rings substantially immune to pressure-related dimensional changes. Because of these features and benefits, the backup rings can establish a very small extrusion gap clearance with the mandrel without risk of heavily loaded metal-to-metal contact. This small extrusion gap clearance allows the Plastic Lined Kalsi Seals to realize their highest pressure potential.
The floating metal backup rings are located axially by a stack of housings and are prevented from rotating by anti-rotation pins engaging the housings. This swivel design eliminates the use of radial O-rings, which cause significant assembly difficulty, and are prone to failure in high-pressure service conditions.
The housings are piloted together by axially short, bind-proof pilots that assure easy assembly. The housings are clamped together with a pattern of bolts and are located with respect to the mandrel by rolling element bearings. The bearing lubricant is retained by outboard rotary oil seals.
During rotation, the hydrodynamic pumping action of the Plastic Lined Kalsi Seals moves a small amount of hydraulic fluid from the hydraulic circuit into the bearing regions. This is accommodated by vent ports that return the pumped fluid to the hydraulic fluid reservoir via a drain hose (not shown). If desired, the vent ports can be connected with cross-drilled holes in the housings. To facilitate higher rotary speeds, the bearing lubricant can be circulated with a small pump to extract seal-generated heat from the mandrel.
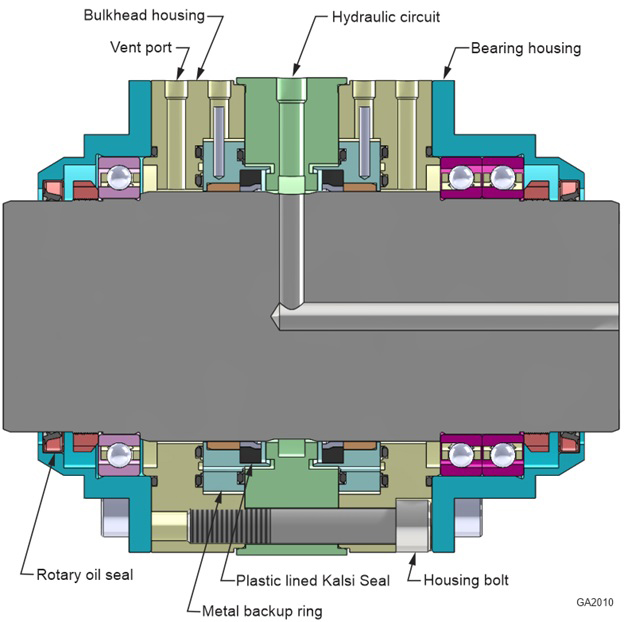
Contact Kalsi Engineering for additional hydraulic swivel design information

Kalsi Engineering, Inc. is a leader in high performance rotary seals and also provides consulting engineering services to various industries. Our patented high pressure hydraulic seals are the result of pioneering research in hydrodynamic lubrication. Our experience in the engineering field makes us a valuable resource for many engineering applications. Whether you are interested in our product lines or need a consultant for your next engineering project, Kalsi Engineering can help you find the best solution for your application. Trust Kalsi Engineering for quality products and advice.
Contact Kalsi Engineering today for a quote, or to learn more about our hydraulic swivel seals, and our design recommendations for high-pressure hydraulic swivels. For available off-the-shelf sizes of high pressure hydraulic swivel seals, see our seal catalog.