We have just completed a 1,500 psi test of a KLS® Seal at a surface speed of 136 feet per minute (Reverse Pressure Test No. 100). The test was performed with a 3.375” PN 668-4 seal. The rotary speed used in the test is equivalent to a 10.375” mandrel rotating at 50 rpm. Plans are underway to manufacture 10.50” KLS Seals, so we can also obtain data from larger diameter seal testing.
The test objective was to determine if the seal could meet the 100-hour minimum test duration established by API 16RCD, “Specification for Rotating Control Devices”. The 100-hour goal was achieved, and we terminated the test after 109.7 hours to inspect the used condition of the seal. Based on the good condition of the seal (see photo below), a 200-hour test is planned. Previous testing has shown that the seal performs well at a surface speed of 543 feet per minute and a differential pressure of 1,000 psi.
During the 1,500 psi test, the bulk lubricant temperature was maintained at 150 to 161° by intermittent, computer-controlled circulation. The purpose of this circulation was to simulate the cooling the lower end of the mandrel of an RCD receives from exposure to drilling fluid. In all testing to date, the running surface has been a ground and polished nickel-based tungsten carbide coating.
Description of the KLS Seal
The KLS Seal is a high performance spring-loaded lip seal for unidirectional rotation. It was designed primarily to serve as an RCD seal. The heel of the seal is lined with extrusion-resistant plastic and has a pattern of hydrodynamic waves. These waves are exposed to the lubricant that is provided to lubricate the bearings that support the rotating mandrel. When differential pressure acts on the spring-loaded end of the seal, the waves are forced into contact with the rotating mandrel and pump a thin film of lubricant into the dynamic sealing interface. This interfacial lubrication inhibits wear and allows the seal to run cooler than it otherwise would, which minimizes modulus loss and promotes high pressure extrusion resistance. As a result, they have considerably more pressure and speed capacity than conventional PTFE lip seals.
During rotation, the hydrodynamic pumping action of the waves causes a small amount of oil to migrate from the low pressure side of the seal to the high pressure side. In the 1,500 psi test described above, the pumping rate was 1.54 ml/hr.
Using the KLS as an RCD Seal
When KLS Seals are used as RCD seals, they are required to contain a high pressure, highly abrasive drilling fluid. This presents a challenge, because lip seals don’t always exclude abrasives well in high differential pressure conditions. The key to using KLS Seals as RCD seals is employing them in pairs, below the bearing stack. Provide a lubricant between the two seals, and then use small pistons or diaphragms to balance the pressure of that lubricant to the pressure of the drilling fluid. This arrangement protects the outboard seal from differential pressure, allowing it to exclude abrasives efficiently.
To discuss using KLS Seals in your rotary shaft seal assembly, call us at 281-240-6500, or send an e-mail. See our shaft seal catalog for available off-the-shelf sizes.
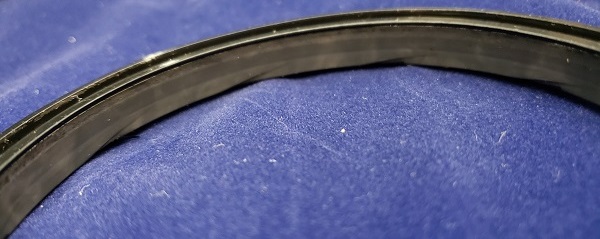