Kalsi Engineering’s new technical paper, “Advancements in Extreme Pressure Rotary Sealing” (OTC-26899-MS), was presented this morning at the Offshore Technology Conference in Houston, Texas. Over the past several years, the authors, Lannie Dietle and Aaron Richie, and several of their colleagues, have been performing research directed at increasing the pressure capacity and life of polymeric rotary seals. Through a combination of innovation, analysis, and testing, they were able to achieve a dramatic increase in the performance of such seals, even when a significant level of shaft runout is present.
The paper begins by describing several key factors that limit the life of polymeric seals in high differential pressure conditions; including adhesive wear, extrusion damage, seal-generated heat, shaft runout and deflection, and the destructive results of inadvertent metal-to-metal contact between the shaft and the seal housing. Next, the paper describes the enabling technology that has allowed them to achieve long operating life in extreme high differential pressure conditions. One part of the technology is a cooler running, higher modulus, more extrusion resistant rotary seal that addresses adhesive wear by operating in a hydrodynamic lubrication regime. Another part of the technology is a mounting arrangement that minimizes the extrusion gap clearance that the rotary seal must bridge, while eliminating the possibility of heavily loaded metal-to-metal contact between the shaft and the seal housing.
After describing the theory of operation of the new technology, the paper reports on a number of tests where the new sealing arrangement achieved PV values in the range of 1.62 to 1.89 million psi x surface feet per minute (sfpm). The 1.89 million PV is about 4.7 times greater than published ratings for conventional high pressure polymeric seals, and was established in a 1,000 hour test at 7,500 to 7,800 psi and 252 sfpm. The seals were still in excellent condition at the conclusion of the test.
The tests were performed in conditions simulating various types of oilfield equipment, such as rotary control devices (RCDs), cementing heads, hydraulic swivels, and high pressure washpipe assemblies. Testing was conducted at pressures as high as 10,000 psi, speeds as high as 540 sfpm, and bulk temperatures as high as 180 degrees Fahrenheit. Some tests were intentionally subjected to 0.010” of dynamic runout.
We are very pleased that Dietle and Richie’s technical paper was selected for presentation at OTC 2016, and commend them on the new high pressure benchmark they have established in the world of polymeric rotary seals. Contact us for additional information.
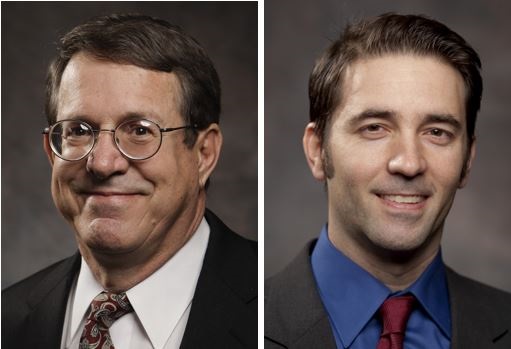