In 2019, Kalsi Engineering was awarded a contract with the Department of Navy (DoN) through the Small Business Innovation Research (SBIR) program to develop and refine flow conditioners for possible use on the Columbia Class submarines and other Navy and non-Navy applications. Flow conditioners are used to diminish swirl and expedite the velocity profile recovery in disturbed flow caused by upstream flow disturbances like elbow, tees, and valves.
Kalsi Engineering successfully completed Round I, II, and III of the Direct to Phase 2 SBIR program and is now preparing for Round IV. Round IV focuses on commercialization for Navy and non-Navy applications.
Due to the operating requirements of Navy submarines, flow conditioners were developed to have the following performance characteristics:
- Generate minimal differential pressure
- Designed to install into existing piping systems
- Operate without producing excessive vibration, noise, and cavitation
As part of the SBIR/DoN project, KEI flow conditioner designs have been refined based on extensive Computational Fluid Dynamic (CFD) analysis and water flow loop testing.
KEI Flow Conditioner Family
KEI has developed and patented a family of flow conditioner elements that can be divided into two general categories: 1) integral conditioner elements and 2) downstream conditioner elements. The classification integral conditioner element includes conditioner elements that are integrated into the pipe bend (e.g., elbow). Downstream conditioners are located downstream of the pipe bend exit or upstream of a pump intake. These conditioner elements can be used separately or together to achieve highly conditioned flow.
KEI integral conditioners provide significant advantages over traditional conditioners in that they reduce the secondary flow that develops in a pipe bend and take advantage of the pipe length associated with the bend to save space. Because the integral conditioners reduce secondary flow in the pipe bend, the flow conditioning requirements at the pipe bend exit are significantly reduced, which ultimately allows for a more compact and effective downstream conditioner achieve highly conditioned flow. The integral conditioner augmented with a KEI downstream conditioner can achieve a highly conditioned flow as close as 5 pipe-diameters from a flow disturbance without producing significant noise or vibration.
Figure 1 shows three KEI designed conditioners and a conventional multi-hole conditioner (MHC). The MHC is not designed by KEI. The MHC conditioner was included in the KEI test matrix for comparison.

Three examples of KEI conditioners (a through c)
and a Zanker Plate Style Conditioner (d)
Conditioner Assessment, Advantages, and Benefits
KEI performed a comprehensive matrix of flow loop testing and CFD analyses to ensure optimal flow conditioning is achieved based on key performance factors, such as differential pressure, cavitation potential, vibration, and sound generation.
KEI performed an extensive CFD matrix to guide initial design and refinement. CFD was used to:
- Assess flow disturbance intensity due to several types of components,
- Perform parametric studies of key features, and
- Evaluate multiple flow conditioner concepts based on velocity profile restoration and improvement in flow metering accuracy.
Flow loop testing was performed to determine the following:
- Flow resistance coefficient (K),
- Liquid pressure recovery factor (FL) to evaluate cavitation potential,
- Velocity profile at 5 and 10 pipe-diameters downstream (measured by 4-axis pitot tube rake),
- Improvement in flow meter accuracy for multiple orifice plates located at 5 and 10 pipe-diameters away from upstream disturbance,
- Flow-generated sound and vibration, and
- Positive effect of conditioners on other downstream components like butterfly valves and check valves.
KEI flow conditioners satisfy the SBIR/DON topic requirement of reducing the required pipe length to achieve fully develop profile by 50%. Most of KEI conditioners achieved fully developed flow with a 66% reduction in required downstream pipe.
The equivalent sound pressure levels based on a frequency range of 500 Hz to 5000 Hz for select KEI conditioners are compared with the result for unconditioned flow (no conditioner) and with the results for the commercial MHC in Figure 2 for a range of flow rates. The equivalent sound pressure is calculated based on a reference pressure of 20 mPa. The results of the sound pressure measurements show that the KEI conditioners have comparable sound levels to Unconditioned Flow. The MHC conditioner (commercial conditioner) produced significantly higher noise levels at higher velocities due to is high propensity to cavitate.
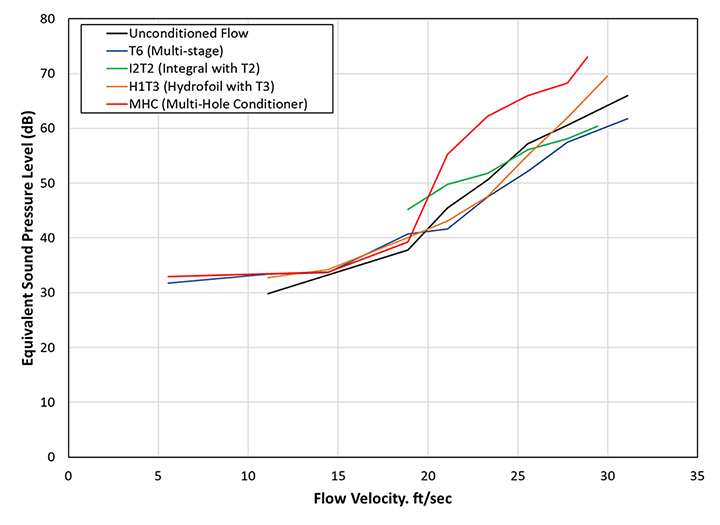
Equivalent sound pressure level based on frequency range of 500 Hz to 5000 Hz. The equivalent sound pressure is calculated using a reference pressure of 20 µPa.
Contact Kalsi Engineering, Inc. to learn more about this innovative technology.
DISTRIBUTION STATEMENT A. Approved for public release: distribution unlimited.