Our KLS-brand high pressure lip seals were originally offered for sale after successful 1,000 psi testing of 3.375” diameter seals at 543 surface feet per minute (sfpm), duplicating the surface speed of a 10.375” RCD seal at 200 rpm. The 3.375” diameter seals have a 0.287” radial cross-section and fit in a 0.250” radial gland depth. An August 10, 2018 blog described a 200-plus hour 1,500 psi test of a 3.375” diameter PN 668-4 KLS Seal at 136 sfpm duplicating the surface speed of a 10.375” diameter RCD seal at 50 rpm. That blog also announced our intent to conduct a similar test with a full size 10.500” KLS-type RCD seal, which has a 0.431” radial cross-section and fits in a 0.375” radial gland depth
Realization of this testing goal involved adapting our 10.500” RCD seal test fixture to accept KLS Seals, and tooling up to manufacture 10.500” diameter seals. Although this required a significant financial commitment, we undertook the testing to make data from full scale testing available to our RCD seal customers because we realize that unforeseen scaling-related surprises can sometimes occur. In a similar vein, we are also currently scaling down to test 1.969” (50mm) KLS Seals.
The goal of the 50 rpm, 1,500 psi test was to determine whether the 10.500” diameter KLS Seal could meet the 200-hour testing goal established by API 16RCD, “Specification for Rotating Control Devices” when used with a 0.015” radial extrusion gap clearance. The test (Full scale RCD seal test no. 38) was terminated at 214.3 hours to observe the condition of the PN 668-39 test seal. At the conclusion of the test, the condition of the used test seal was excellent, as shown in Figure 1. The seal lubricant was an ISO 320 viscosity grade synthetic hydrocarbon lubricant, and the average hydrodynamic pumping related lubricant leak rate of the test seal was 0.52 ml/hr.
The test setup is shown in Figure 2. The test was configured to simulate the pressure retaining inboard seal of an RCD that employs two lip seals, with the lubricant pressure between the seals balanced to the wellbore pressure. In such an arrangement, the outboard lip seal is exposed to the abrasive wellbore fluid but protected from high differential pressure, and the inboard seal is exposed to high differential pressure but protected from the abrasive wellbore fluid.
The high-pressure test fluid was an ISO 320 viscosity grade synthetic hydrocarbon lubricant contained by the test seal and a PN 682-21-303 RCD seal. The low-pressure lubricant for the test seal was contained by another KLS lip seal. A slowly circulating low pressure coolant was provided below the PN 682-21-303 seal and above the uppermost KLS Seal, to control the heat generated by the four rotary seals required by the test setup. During the test, the high-pressure lubricant below the test seal averaged 109.9°F and the low-pressure lubricant above the test seal averaged 98.7°F.
The PN 682-21-303 RCD seal was also exposed to 1,500 psi differential pressure and survived the test in excellent condition. It was mounted in a non-floating seal carrier that defined a 0.010” radial extrusion gap clearance.
To discuss using Kalsi Seals in your RCD, contact our staff by e-mail or telephone; For available off-the-shelf sizes, see our shaft seal catalog.
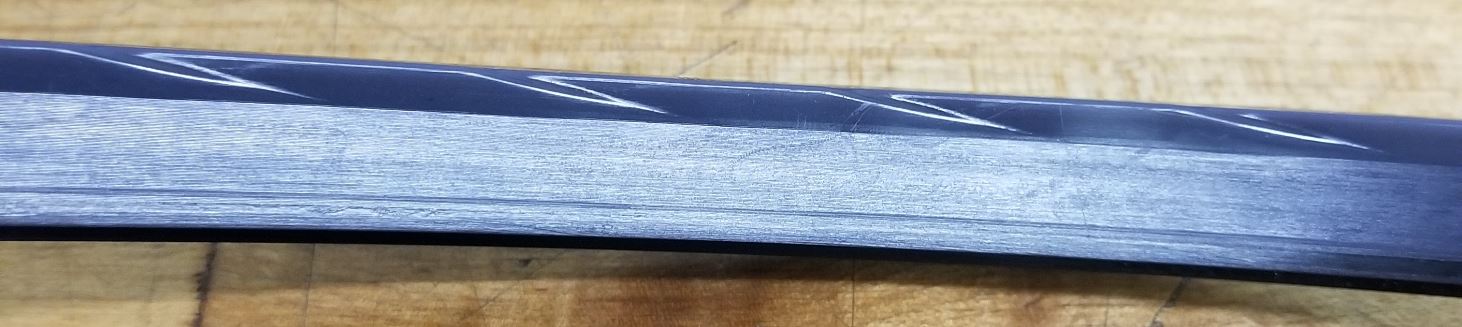
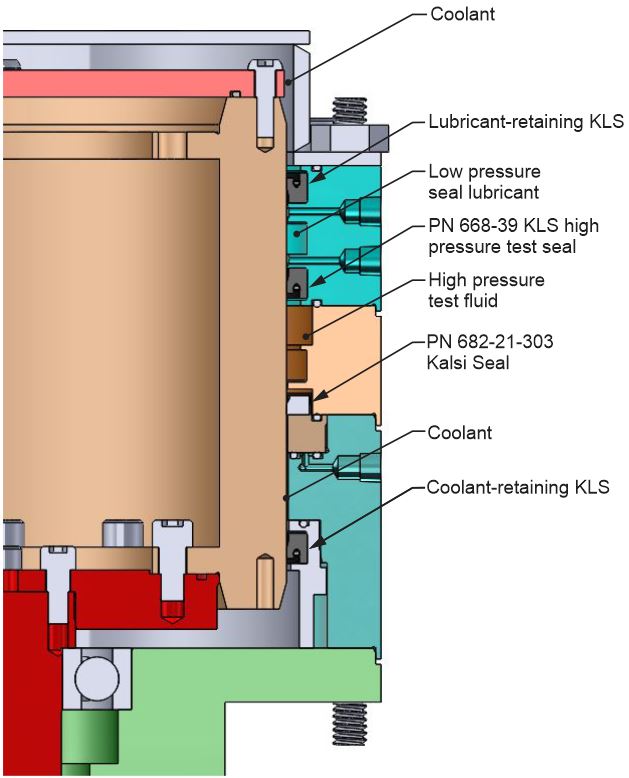