Assessment of a Large Butterfly Valve Experiencing Hydrodynamic Torque Fluctuations
Large butterfly valves are used in the circulating water system of nuclear power plants. These valves are often 84-inches or larger and are of symmetric or single offset disc design. When large butterfly valves are positioned at a disc opening angle of approximately 70° to 90°, the valve disc can experience hydrodynamic torque fluctuations that approach or exceed the magnitude of the time-averaged value. The hydrodynamic torque fluctuations generate varying stresses in the torque train components that can cause fatigue failure.
Hydrodynamic torque fluctuations occur when unsteadiness in the flow causes fluctuations in the differential pressure field acting on the disc. The pressure fluctuations cause time-dependency in the magnitude of the flow-induced force and location of the line-of-action. Changes in the location of the line-of-action can strongly affect the hydrodynamic torque, especially if the line-of-action crosses from one side of the stem centerline (i.e., center-of-rotation) to the other. When the line-of-action crosses the shaft centerline a reversal in hydrodynamic torque direction occurs.
Hydrodynamic torque reversals can cause the disc to flutter. Disc flutter can result in impact loading in the torque train components. Because high inertial forces can exist during impact loading, impact loading can greatly increase the magnitude of the alternating stress in the torque train components (e.g., disc pins, shaft, or quarter-turn gear box components) and accelerate fatigue related damage.
KEI™ provided engineering support to several nuclear power plants to assess disc flutter that caused multiple failures of the torque train components. In the example below, the shape and structure of the upstream pipe bend — which were of a multifaceted design — introduced abrupt changes in flow path cross-section and flow direction. Flow separation from the upstream pipe-bend corners caused broad spectrum vortex shedding and a strong vortex tube to extend beyond the butterfly valve disc. The combined effect of the rough flow associated with the vortex tube and the buffeting of the disc caused large hydrodynamic torque reversals that resulted accelerated damage of various torque train components.
KEI performed transient CFD analyses of the subject valve at key disc positions to better understand the development and interaction of the vortex tube and shed vortex structures with the disc. The CFD analyses included the upstream piping and a section of the header. An image of the vortex structures around the disc based on CFD prediction is shown as Figure 1.
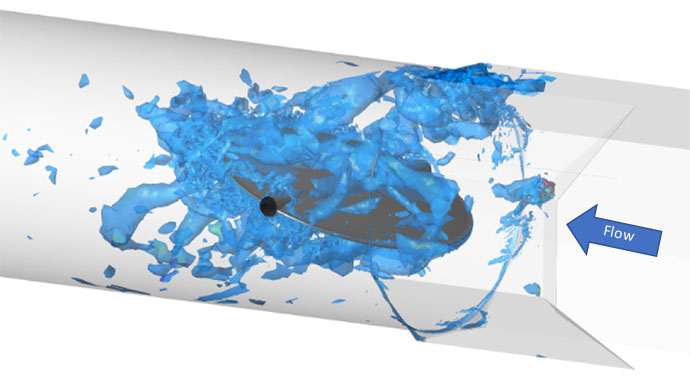