Mud Motor Seals
Mud Motor Description
Mud motors are used for various drilling tasks such as straight hole, horizontal, directional and short radius oilfield drilling, river crossings and other utility drilling. They are connected to the drillstring to rotate and steer the drill bit. Rotation is provided by a power section, which is typically a positive displacement motor that is driven by drilling fluid circulation. Axial and radial drilling loads are reacted to the drillstring by the bearings within the sealed bearing assembly.
For directional drilling, a small bend angle is provided between the power section and the bearing assembly. This bend angle gives mud motors the ability to selectively drill curved or straight holes. Drillstring rotation produces a straight, slightly oversized hole. In the absence of drillstring rotation, the hole curves in the direction of the bend.
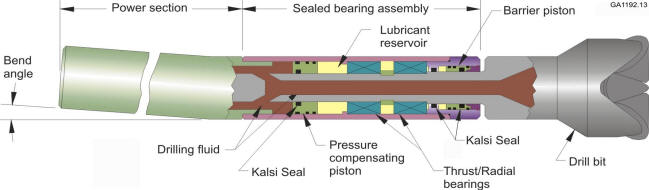
Hydrodynamic Mud Motor Seals
Kalsi Seals® are a family of patented, one-piece rotary seals that provide hydrodynamic lubrication to minimize seal and shaft wear, and to accommodate high differential pressure. They are used for lubricant retention and contaminant exclusion. They were originally developed for the harsh and unforgiving oilfield downhole drilling environment, and provide an effective solution to the severe service conditions found in many different industries.
Sealed bearing advantages (compared to mud-lubricated assemblies) are:
- Compact size, which facilitates short radius drilling
- Reduced bearing friction and eliminating mud bypass provides greater efficiency
- May employ off-the-shelf conventional bearings
- Reduced repair and maintenance costs
Surface pumps are used to circulate the drilling fluid to flush rock cuttings to the surface for disposal. The drilling fluid flows down through the bore of the drillstring, exiting into the annulus of the well through the jets (not shown) in the drill bit. The cuttings are flushed up the annulus of the well by the returning drilling fluid. The annulus pressure is substantially lower than the drillstring bore pressure due to the pressure drop that occurs as the drilling fluid passes through the drill bit jets.
Mud Motor Seal Locations
Sealed bearing mud motors have several rotary seal locations, and all are critical to reliability. A mud seal in an axially floating pressure compensation piston is used to balance the lubricant pressure to the drillstring bore pressure. A rotary seal in a fixed location is used to withstand the high pressure differential between the lubricant and the well annulus pressure. A mud seal in an axially floating barrier piston protects the high pressure seal from the drilling fluid.
The rotary seals in the two floating pistons are exposed to the severe abrasive content of the re-circulated drilling fluid, and all seal locations are subject to shaft motion resulting from drilling forces and power section rotor thrust and nutation. Each location has its own unique challenges, including high differential pressure at the fixed location seal, and reversing pressure and sliding motion at the piston-mounted mud seals.
State of the Art Oilfield Seals
The lack of reliability and short life of conventional seals had previously limited the acceptance of sealed bearing assemblies, but the Kalsi Seal has allowed them to attain widespread use. The reliability, ease of maintenance, and economics of the Kalsi Seal have been proven by the thousands of motors that use them today. Kalsi Seals represent the state of the art in mud motor seals. Runs in excess of 500 hours have been achieved by several oilfield customers. Guidelines for implementing Kalsi Seals in mud motors and other oilfield seal applications are included in the Kalsi Seals Handbook™. For available sizes of mud motor seals, see our shaft seal catalog.
Contact us to learn more about our mud motor seals and how we can help you.