RCD Seal Training
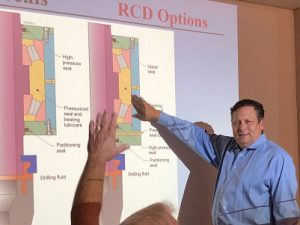
As a leading manufacturer of rotating control device (RCD) seals, Kalsi Engineering offers training about how to implement such seals in RCDs. The training is intended for mechanical engineers, designers, and managers who are responsible for developing and maintaining RCDs.
The duration of the training depends on the desired scope of subject matter. From a rotary seal standpoint, RCDs can be grouped into two major types: those with a pressurized lubricant supply, and those without. We manufacture seals for both types of RCDs and can include a discussion of one or both types in the training course. The training is offered free of charge and can be provided at your location or ours, or via web conference. Contact us to schedule training, or to learn more about our high-performance RCD seals.
Implementing Seals in RCDs without a Pressurized Lubricant Supply
The training for RCDs without a pressurized lubricant supply includes a discussion of the types of seals that are available for such service, their principles of operation, and their construction and performance differences. It also provides an overview of the optional ways of implementing such seals in RCDs.
If relevant to customer objectives, our development and testing experience with a valve that returns hydrodynamically leaked lubricant to the bearing chamber is also included. This valve, which is available for licensing, was developed with the objective of enabling a leak-less RCD design.
Implementing Seals in RCDs with a Pressurized Lubricant Supply
The training for RCDs with a pressurized lubricant supply includes a discussion of the high and low-pressure seal locations in an RCD. We describe the operational challenges faced at each location and the design tradeoffs involved in selecting the location of the high-pressure seal. This leads into a discussion of methods for pressurizing the seal lubricant, including hydraulic pressure control, piston amplifiers, and the use of constant displacement pumps with rotary lip seals.
Following the discussion of the high and low-pressure seal locations, the training includes a description of the RCD seal designs that are available for each location, including a description of construction differences and performance attributes and tradeoffs.
If appropriate to the customer’s objectives, techniques for obtaining the highest possible pressure capacity are discussed, including the use of laterally floating seal housings and pressure staging. If desired, a separate training class that focuses on how to design floating seal carriers can be provided.
Topics Common to Both Types of RCD Seal-Related Training
Some topics are common to both types of RCDs. For example, regardless of the type of RCD being discussed, we begin the training with a brief introduction to Kalsi Engineering, for the benefit of individuals who may not be familiar with our company along with a description of the operating principle for Kalsi Seals.
A mandrel-related portion of the training covers various topics, including hard coatings for wear resistance and appropriate tolerances and surface finish requirements. This section of the training also covers design of the seal installation path, including the installation chamfer, to avoid seal damage during installation onto the mandrel.
A seal housing-related portion of the training reviews critical features of the grooves that locate the RCD seals. Topics include groove surface finishes, radial extrusion gap clearance, axial extrusion gap width, the extrusion gap corner, and techniques for counteracting pressure-related component deformation. This part of the training also covers techniques for improving mandrel-to-seal housing concentricity.
A heat transfer portion of the training begins by explaining why heat concentrates in the seal track region of the mandrel and covers design practices that promote cooler seal operation. Topics include the heat transfer interruption caused by sleeves and optional cooling circulation for higher speed, higher pressure operating conditions.
A bearing-related portion of the training presents several potential bearing related issues. Topics include designing shoulders for ease of disassembly, avoidance of misalignment-related shaft binding, the perils of inadequate thrust bearing support, the implications of spherical roller thrust bearing orientation, and the potential for spacer-related binding.
A lubricant-related portion of the training discusses the preferred class of seal lubricants, how to achieve a good initial lubricant fill, and why an effective lubricant fill is so important.
If appropriate to the customer’s objectives, the training can also include a discussion of pressure compensation piston design. Discussion topics include piston guidance, avoidance of the sticky drawer effect, the negative implications of large diameter annular pistons, and how to design the mud-side extrusion gap.
Training Objectives
At the conclusion of the training, your engineers and designers will have a better understanding of the types and capabilities of the RCD seals we manufacture, and how they can be implemented in RCDs. They will also have an understanding of various implementation details related to mandrel and seal housing design, and an understanding of overall RCD design and assembly factors that influence the performance of the rotary seals. They will also have a general understanding of the material in our rotary seal handbook that is relevant to RCD design, so they can access that material during future design activities.
Click here to review a complete list of Kalsi Seal-related training classes.