Rotary Valve Actuators for Kelly Valves
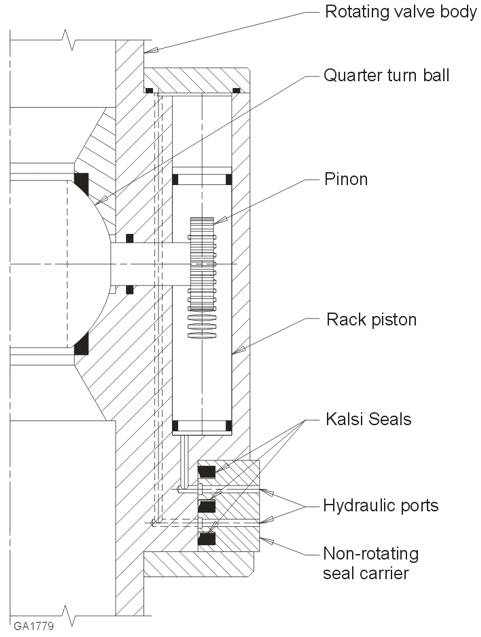
A Kelly valve is a ball valve that is installed in-line with the drill string of an oil well. When used as an upper Kelly valve, the valve is closed when needed to control the pressure of a blowout. When used as a lower Kelly valve, the valve is closed to prevent drilling fluid loss during periods when the Kelly is disconnected. When open, the Kelly valves allow free flow of the drilling fluid. A Kelly valve is also referred to as a “Kelly cock”, “drill pipe safety valve”, or “drill stem safety valve” (DSSV).
A hydraulic rotary valve actuator, also known as a rotary hydraulic actuator or a Kelly valve actuator, is used to open or close the Kelly valve during drill string rotation. As shown in the schematic, a hydraulically operated rack and pinion arrangement is used to turn the stem and ball of the Kelly valve. The hydraulic fluid pressure is transmitted to the rack piston of the valve actuator via three rotary seals that are mounted in a non-rotating seal housing and define two hydraulic channels. In other words, the rotary valve actuator incorporates a compact hydraulic swivel that communicates hydraulic pressure to one end of the rack piston to open the Kelly valve, and communicates hydraulic pressure to the other end of the rack piston to close the Kelly Valve.
Why are Kalsi Seals used in hydraulic swivel applications?
Kalsi-brand rotary seals provide a significant reliability advantage in swivel-type applications such as Kelly valve actuators. This increased reliability is provided by a special lip design that introduces a thin film of hydraulic fluid between the lip and the mating shaft surface during rotation, allowing the lip to hydroplane on the oil film. This hydroplaning action minimizes friction, which reduces seal-generated heat and wear and improves seal life, helping to ensure reliable opening and closing of the Kelly valve.