Introduction
To help our customers meet their high pressure rotary control device (RCD) goals, we have performed characterization testing of our 10.50” (266.7mm) PN 682-20-318 Plastic Lined™ RCD seals. The testing was performed at several different pressures, including duration testing at 2,300 psi (15.86 MPa). The 2,300 psi test pressure simulates a lubricant overpressure type RCD operating with 2,000 psi (13.79 MPa) wellbore pressure and 300 psi (2.07 MPa) lubricant overpressure.
Although the best high pressure performance can be achieved when the seal is supported by our patented floating backup ring (U.S. Patent 9,429,238), this testing was performed with conventional non-floating seal carriers that define a relatively large 0.020” (0.51mm) nominal radial extrusion gap clearance with respect to the rotating shaft. The combination of high pressure and a large extrusion gap is an extreme operating condition for a high pressure rotary seal.
The testing shows that our Plastic Lined Seals™ can tolerate a high differential pressure and large extrusion gap beyond the 100 hour minimum duration specified in API 16 RCD. As seen in the photograph below, one of the rotary seals was still in new condition and the other had only moderate wear after 187 hours of high pressure operation.
Test fixture configuration
The test fixture, which is illustrated below, simulates the pressure-retaining seal location of an RCD, and tests a pair of rotary seals simultaneously. The test pressure was applied to an ISO 220 viscosity grade lubricant that is located between the rotary seals. This viscosity was selected for its compatibility with the heavily loaded bearings of an RCD.
In an RCD, the lower end of the rotating shaft is exposed to the circulating drilling fluid, which establishes a temperature boundary condition on the RCD surfaces that are exposed to the fluid. This thermal effect was simulated by circulating a cooling fluid outboard of the lower seal at a flow rate of 2 gpm. As a result of this circulation, the lower seal operates in a thermal condition that is similar to an RCD that uses a circulating bearing lubricant for cooling purposes, and the upper seal operates in a thermal environment that is more similar to an RCD that does not circulate the bearing lubricant.
The shaft runout was 0.007” at the upper seal location and 0.003” at the lower seal location.
High pressure rotary seal configuration
The PN 682-20-318 rotary seals are direct compression seals that incorporate a high modulus plastic liner for extrusion resistance. This plastic layer is energized against the shaft by a compressed elastomeric seal body. The seals incorporate our patented Type A Enhanced Lubrication™ wave pattern. During shaft rotation, this wave pattern pumps enough lubricant between the shaft and the plastic layer of the seal to cause the plastic layer to hydroplane. This hydroplaning action dramatically reduces seal friction and seal-generated heat, allowing the plastic layer to retain maximum strength, and minimizing adhesive wear. This hydroplaning action produces a positive lubricant leak rate that decreases as pressure and temperature increase. In the absence of rotation, the pumping action and associated leak rate cease.
The high pressure portion of the testing
The 2,300 psi (15.86 MPa) portion of the test was the final stage of the high pressure seal test. During this stage, the shaft was rotated at 100 rpm. Cooling fluid was circulated below the lower rotary seal at 2 gpm. No circulation was present between the rotary seals, or above the upper rotary seal. After 182 hours of testing, a rise in running torque was detected, and the test was terminated for seal inspection. The rotary seals were still sealing statically after the test was terminated.
The lower seal was unworn at the conclusion of the test, and the upper seal had modest wear over a band about 0.07” (1.78mm) wide. This difference in seal condition illustrates the significant benefit resulting from even modest coolant circulation. We associate the observed rise in seal torque as being the result of the wear of the upper seal.
The hydrodynamic pumping related leak rate during the 2,300 psi (15.86 MPa) portion of the test was 4 ml/hour per seal.
The medium pressure portion of the testing
Knowing that pumping-related seal leakage increases as pressure is reduced, we tested the seals at lower pressures before conducting the 2,300 psi (15.86 MPa) portion of the test. At 1,000 psi (16.9 MPa), the leak rate per seal was 22.5 ml/hour; at 1,500 psi (10.34 MPa), the leak rate per seal was 11.5 ml/hr.
During three hours of 1,000 psi operation, the average temperature of the region above the upper seal was 117°F, and the average bulk lubricant temperature between the seals was 132°F. During two hours of 1,500 psi operation, the average temperature of the region above the upper seal was 138°F, and the average bulk lubricant temperature between the seals was 156°F.
The low pressure portion of the testing
In the low pressure portion of the testing, coolant was circulated above the upper rotary seal, and below the lower rotary seal, to maximize the hydrodynamic pumping related leak rate by minimizing the operating temperature. The lubricant pressure was 300 psi (2.07 MPa), simulating an RCD with zero psi wellbore pressure and 300 psi lubricant overpressure. New seals were used for this portion of the testing. At 100 rpm, the leak rate per seal was 99.5 ml/hr, and at 180 rpm, the leak rate per seal was 345.5 ml/hr.
Interpretation of test results
This test indicates that a lubricant overpressure type of RCD with moderate lubricant circulation for cooling purposes can operate reliably at 100 rpm with a wellbore pressure of 2,000 psi (13.79 MPa), with a readily achievable extrusion gap clearance. For example, the test can be interpreted as validating a high pressure RCD design having a nominal radial extrusion gap clearance of 0.010” (0.25mm), and nearly 0.010” (0.25mm) shaft misalignment. The test also suggests that our RCD seals have applicability as swivel seals in high speed, high pressure hydraulic swivels, where much smaller extrusion gaps are readily achievable.
This test also suggests that it would be desirable to place a low pressure rotary seal outboard of the pressure-retaining seal, so that the increased hydrodynamic pumping related leakage that occurs in low pressure conditions can be captured and returned to the lubricant reservoir. This leakage capture arrangement is covered by US Patent 8,505,924, which is available under license to users of Kalsi-brand rotary shaft seals.
For additional information on our highly capable high pressure RCD seals or to request a quote, call 281-240-6500, or contact us by e-mail. For available sizes, see our shaft seal catalog.
Future testing plans
In the near future, we will be testing our high pressure RCD seals in non-floating seal carriers that define a 0.010” (0.25mm) nominal radial extrusion gap clearance. We will also be testing RCD seals that are made with our robust -303 plastic-lined material combination.
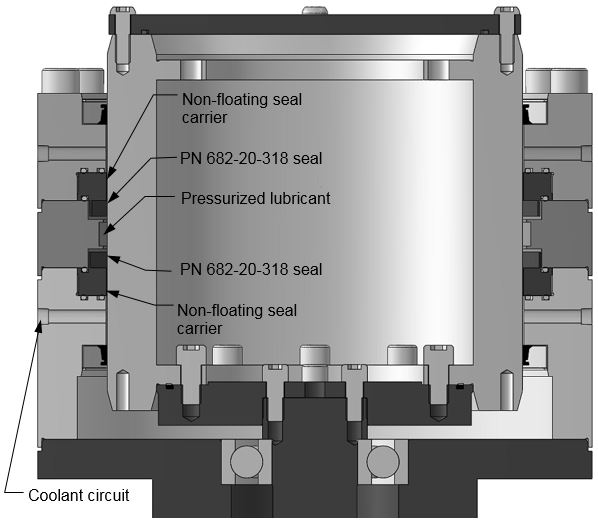
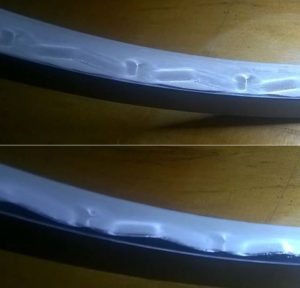